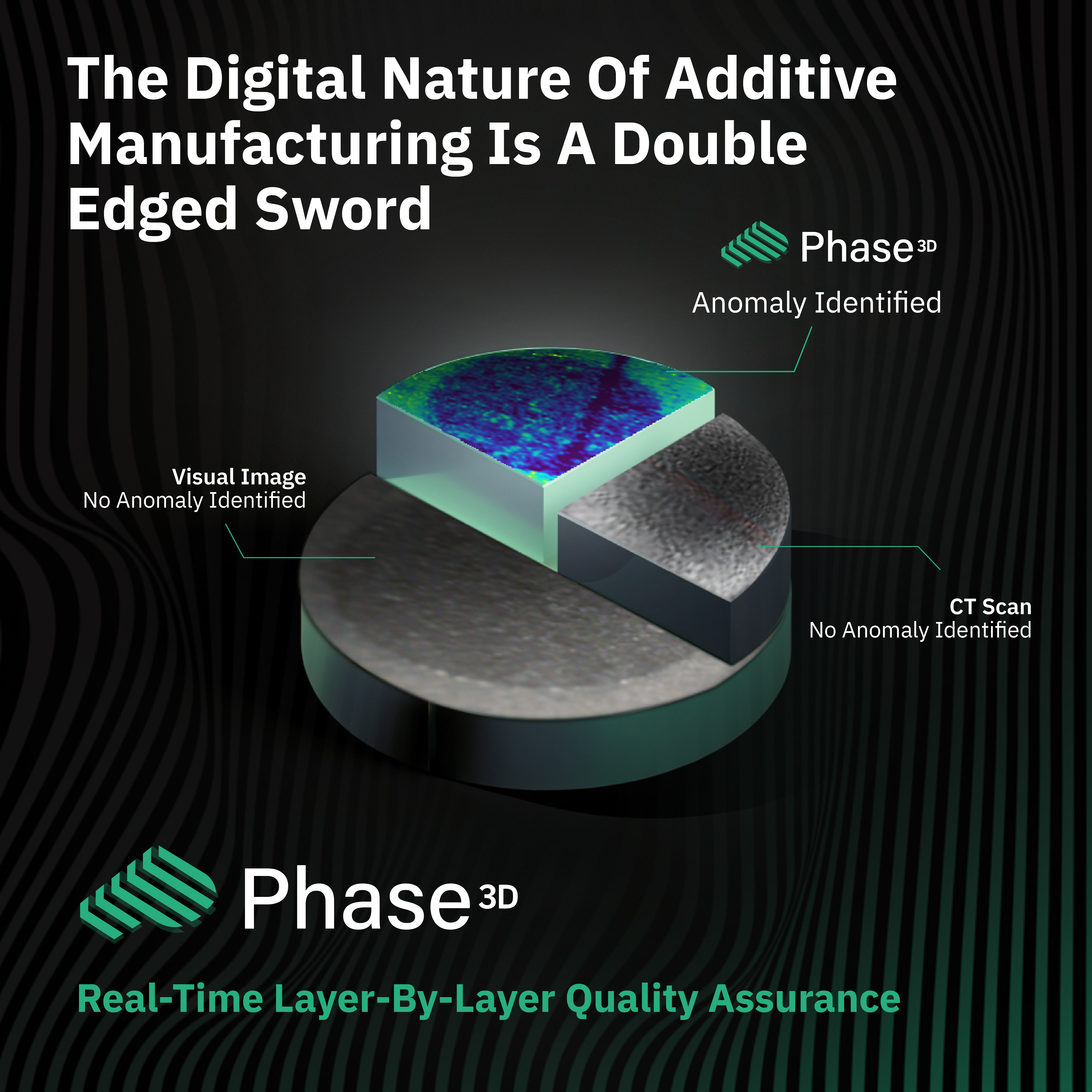
Additive manufacturing has revolutionized how we think about design, production, and innovation. Born in the late 1980s, AM became a game-changer in industrial applications by the 2000s, 2010s, to today. Yet, the same digital-first approach that gives AM its strength also introduces its unique challenges—making it a true double-edged sword.
The Challenges of Digital Evolution
Traditional manufacturing methods, like casting, rely on long-established processes. Cast parts, for example, often contain significant internal defects or pores. If you were to CT scan a cast part, you likely wouldn’t approve it for critical applications if put to the same specification as an aerospace metal AM part. However, these methods have the advantage of decades of data and proven qualification processes.
In contrast, AM’s timeline has required parts to meet—if not exceed—the performance of their traditional counterparts, because the technology comes without the same historical data for validation. The digital nature of AM enables unprecedented complexity in design but complicates qualification and validation. How do you ensure that an AM part will perform reliably under stress when the process itself is not exactly the same during every build?
Why In-Situ Inspection Is Essential
The solution lies in leveraging AM’s digital capabilities for better oversight. In-situ inspection provides real-time data during the build process, allowing manufacturers to inspect and validate part quality as it happens. This eliminates the guesswork and ensures that parts meet rigorous performance standards, even for the most demanding applications.
By integrating in-situ inspection into AM workflows, manufacturers can address the inherent challenges of digital manufacturing while maximizing its benefits. It’s not just about detecting defects—it’s about ensuring confidence in every layer, feature, and micron of the part.
The Future of AM Qualification
As AM continues to evolve, so too must our approach to part qualification. The digital-first nature of AM is both its greatest strength and its most pressing challenge. By embracing tools like Fringe Inspection™, we can navigate the double-edged nature of AM, providing real-time insights that ensure precision, reliability, and confidence in every part. Fringe Inspection™ is the key to unlocking AM's full potential for industries where performance is critical.